Call Us Now
Mon - Saturday
9:30 AM - 6:30 PM
Beer Manufacturing Project :
Brewhouse System, Fermentation System, Cip System, Cooling System, Control System.
1.BREW HOUSE SYSTEM :
Repair all type of Company refBrew house system consists of Mash Tun, Lauter Tun, Boiling Kettle, Whirlpool kettle, Hop Dosing Equipment. The main equipment adopted international quality standards of sanitary 304 stainless steel, to deal with the tank by plasma cutting, pure AR-shielding welding, and mechanized automatic polishing machine.
Our scientific Dimple jacket production technology can utmost ground realizes the effect of heat conduction, use high quality rock wool or polyurethane materials to insulation for the inner tank, and effectively prevent heat energy leakage from the tank. Advanced Lauter Tun raker system and automatic hydraulic lifting technology, can ensure mash filter uniform and comprehensive.
The brew house system could be included two vessels brew house, three vessels brew house and four vessels brew house includes mash / Lauter Tun and kettle / whirlpool tank. Three vessels include mash tank, Lauter Tun and kettle / whirlpool tank. Four vessels include mash tank, Lauter Tun, boiling kettle and whirlpool tank. The capacity is bigger, the vessel is more and you can also choose the multiplayer assembly from, improve the working efficiency.
The scarification system heating has many forms, such as steam heating, electric pipe heating, direct fire heating, heat conducting oil heating and so on.
2.FERMENTATION SYSTEM :
Fermentation system is made up of Fermentation Tank and Bright Beer Tank quantities are based on customer’s request. According to different fermenting request, structure of fermentation tank be designed accordingly. Generally Fermentation Tank structure is dished head and cone bottom, with Polyurethane installation and dimple cooling jackets. There is a cooling jacket on tank cone section; columnar part has two or three cooling jackets. This not only can meet the relevant requirements of cooling, guarantee cooling rate of fermentation tank, also help to precipitation and the yeast.
Tank internal and external wall are made of international quality standards of sanitary 304 stainless steel, the Polyurethane insulation thickness between the inner and outer is 50-200 mm. conic bottom install inlet outlet pipes. Tank installation cleaning system, tank roof device, tank bottom device, rotating wine outlet tube, inflatable device, liquid level meter, sampling valves and other supporting valve, equipped with temperature sensor, with the help of PLC auto-control, the equipment can reach to automatic and semi-automatic control. The height of conic bottom is a quarter of the total height. The ration of tank diameter and height of tank is 1:2-1:4, the cone angle usually between 60°-90°.
3.CIP SYSTEM :
CIP cleaning system include lye tank, Hydrogen Peroxide tanks and as line valves, if the tank volume is small, the tank can be fixed on trolleys, so it’s easy to clean brewing system. Alkaline cleaning can removed the fat and protein by saponification, to improve product safety. After the CIP treatment, clean bright surface, no water, no savor, no dirt. And device is easy to operate, strong security.
4.COOLING TUNNEL :
The cooling system includes Chilled Water Tank, refrigerating machine and other line valves equipment, Beer refrigeration system is mainly used for cooling the saccharifying wort and fermentation, it plays an important role in the whole process of brewing beer. Our factory refrigerating machine is home famous brand with stable performance, excellent refrigerating effect, and low accident rate. Optimum allocation of refrigerating system can greatly reduce the wastage of the energy. Ensure the stable operation of the beer brewed.
5.Control System :
The PLC controlling system includes Delta/Siemens programmable controllers, industrial personal computer and other auto-controlled components; the heating and cooling are fully automatic control, and it can also be hand controlled on the operation platform. The technological parameter can be programmed and set automatic or manually according to customer’s requirement or the technological requirements for different objectives.
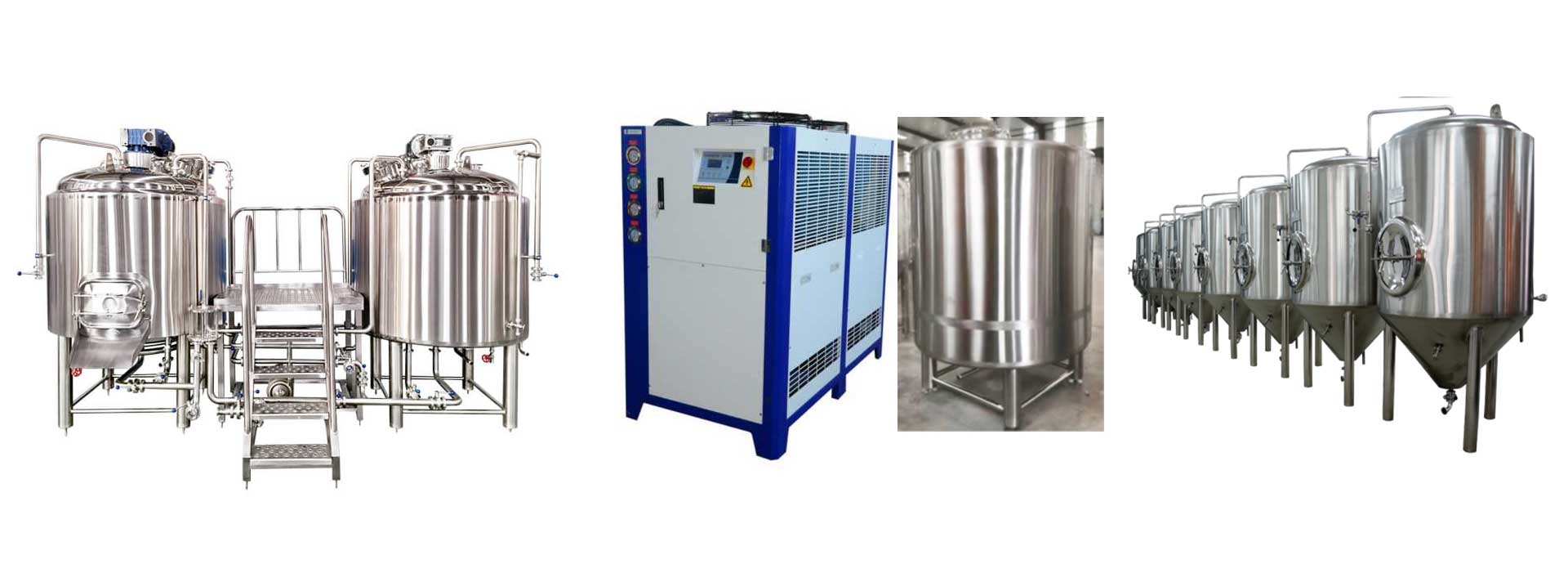
Juice & Milk project.
Sugar Syrup Preparation for Tank for Juice, Sugar Filter Press for Juice, CIP System for Juice, PHE System for Juice, Skid Mounted Juice Pasteurizer, Homogenizer For juice, Cooling Tunnel for Juice.
Juice Rinsing, Filling & Capping Machine:
Rinsing
Inside of bottles are rinsed by spraying water or air or both. Empty bottles are transferred into the rotary rinsing section by an inlet neck guide. The bottles are held from their neck and inverted by a guide rod along their axis. After being sprayed internally, the bottles continue to move inverted for a while to drain the rinse water, after which they are turned back to the upright position. The nozzles have “No Bottle – No Spray System” which is activated only by the presence of bottles, sensed at the in-feed spider. The option of attachment of an independent rinser machine is possible, to build a mono-block machine of Rinser filler crowner / capper for bottles.
Filling
The filling operation is by gravity. RECIRCULATING VALVE (mechanical valve) which features 10-15% juice temperature upto the tip of the filling valve constant, hence maintaining product safety without any manual intervention. This valve has a bottom close design and has a zero drip feature after the filling operation, it has CIP features & fills at a very high speed due to its excellent design. The other option of the valve is a top close straight valve with recirculating from the filler bowl by means of a pump this is also an efficient cost saving design. An option of flow meter along with pneumatic actuator valve (electronic filling valve) for extremely accurate fill can in now available.
Capping
Different capping heads can be installed on the mono-block machine to apply plastic screw caps, aluminium caps and metal crown corks. Two types of caps can be applied on the same machine in order to have capability to apply different closure.
1. SUGAR SYRUP PREPARATION FOR TANK FOR JUICE :
- Fro Storage / Blending / Dispensing / Standardization / Sugar Syrup Preparation.
- Suitable collect, store, dispense and blend liquids like pulp, juice, beverage, sugar syrup can be fitted with stirrer or blending device, temperature indicator, liquid level indicator and CIP spraying head.
- Tanks can be fabricated in SS 304 / 316 in single / double / triple layer with or without steam jacket insulation.
- The tanks are welded with smooth inner walls and are finished upto 150 grit finish and are hydraulic tested.
- Available in capacities from 100-L – 15-KL interconnected with centrifugal / screw pumps.
2. SUGAR FILTER PRESS FOR JUICE :
The unfiltered liquid is fed into the filter under positive pressure, where liquid travels in downwards direction and finds its way through opening on sides of the filter plates. As the liquid pressure increases, the filter media holds the foreign particles and allows only clear filtrate to pass through the central channel formed by interlocking pressure cups to the outlet is reached or continued until the cake holding capacity of the unit is reached or until the filtrate rate becomes too slow owing to cake resistance.
- Horizontal plate filter press is enclose construction, preventing evaporation, oxidation, leakage and fumes escaping from product.
- Filter Plates are available in two sizes. Deep plate for large percentage of cake holding capacity and shallow plate for small percentage of cake holding capacity.
- The horizontal filter plate even thickness of cake prevents the cake dropping as well as cracking, thus assuring better filter quality.
- The Filtration area cake holding capacity can be increased or decreased according to requirement.
3. CIP SYSTEM FOR JUICE :
Herculean Packaging Solution design and manufacture automatic, cost efficient cleaning-in-place (CIP) system used for cleaning process equipment such as filling machines, pasteurizers, sanitary pipes, tanks, plate heat exchanger etc. with food safety being the number one priority
Herculean Packaging Solution
CIP system are supplied on frame mount with a wide range of capacities, CIP circuits, bespoke software and recipes, Herculean Packaging Solution CIP units are designed for 2, 3, or 4 tank systems and from 1 to 4 pressure lines depending on number of circuits and CIP requirements. Each pressure line include a CIP pump, circulation tank, heat exchanger, process valves, flow meter, conductivity meter, sensors and all necessary internal piping and wiring.
Herculean Packaging Solution
CIP unit automatically controls the cleaning time, detergent temperature, flow and concentration records these parameters continuously and for each cycle for tractability. Available semi & fully Automatic Models, Capacity as per Requirement.
4. PHE SYSTEM FOR JUICE:
A plate heat exchanger is a type of heat exchanger that uses metal plates to transfer heat between two fluids. This has a major advantage over a conventional heat exchanger in that the fluids are exposed to a much larger surface area because the fluids spread out over the plates. This facilitates the transfer of heat, and greatly increases the speed of the temperature change. SS plate heat exchangers are made of 100% stainless steel and provide efficient heat transfer with a small footprint.
They are maintenance free and provide a long service lifetime. They are suited in applications which put high demand on cleanliness, applications where aggressive Medias such as ammonia are used or where copper and nickel contamination is not accepted. Can handle very high temperatures or extremely high pressure.
5. SKID MOUNTED JUICE PASTEURIZER:
In beverage processing / pasteurization plants process parameters are more or less same, heating the product up to the required pasteurization temperature, and it can be filled in hot condition or in case the filling is required in PET bottles of normal grade the product needs to cooled and filled, with proper holding.
However, the type of processing plant varies based on the products, clear juice like Apple, Grape, and Lemon etc. can be processed with plate heat exchangers and viscous products like Mango, Guava etc. needs to be processed with corrugated tubular heat exchangers.
So in order to process all types of beverages in one plant, we recommend corrugated tubular heat exchangers based pasteurization plant. However we manufacture both the heat exchangers and pround to have a list of satisfied customers with both system to install and exchanger modularity.
6. HOMOGENIZER FOR JUICE:
Homogenization is a process which makes the blended beverages having uniform quality. it is not process part of the beverage processing but product specific process. Where fibrous juices/pulps like Mango, Guava, homogenizers with product specific. Homogenizing devices to meet the process requirement
Useful for enhancing the consistency, stability, uniformity, viscosity, absorbency, brightness and homogenizer for fruit juice.
7. COOLING TUNNEL:
Cooling tunnel is used for getting hot bottles from 90 / 95 degrees to the room temperature of 30 – 35 degrees. It is used for hot filled bottles like juice. After the hot fill product and pasteurizing fast effective product cooling is required in order to maintain the product taste, appearance and other important characteristics that are important to your products market potential. Inside the machine, the bottles and the cans lie on a plastic chain and thanks to an external gear motor go forward in the various sections encountering the upper showers, at different temperatures, until reaching the exit. The feed rate of the bottles and cans be set from an operating panel that allows to vary the duration of the cycle.
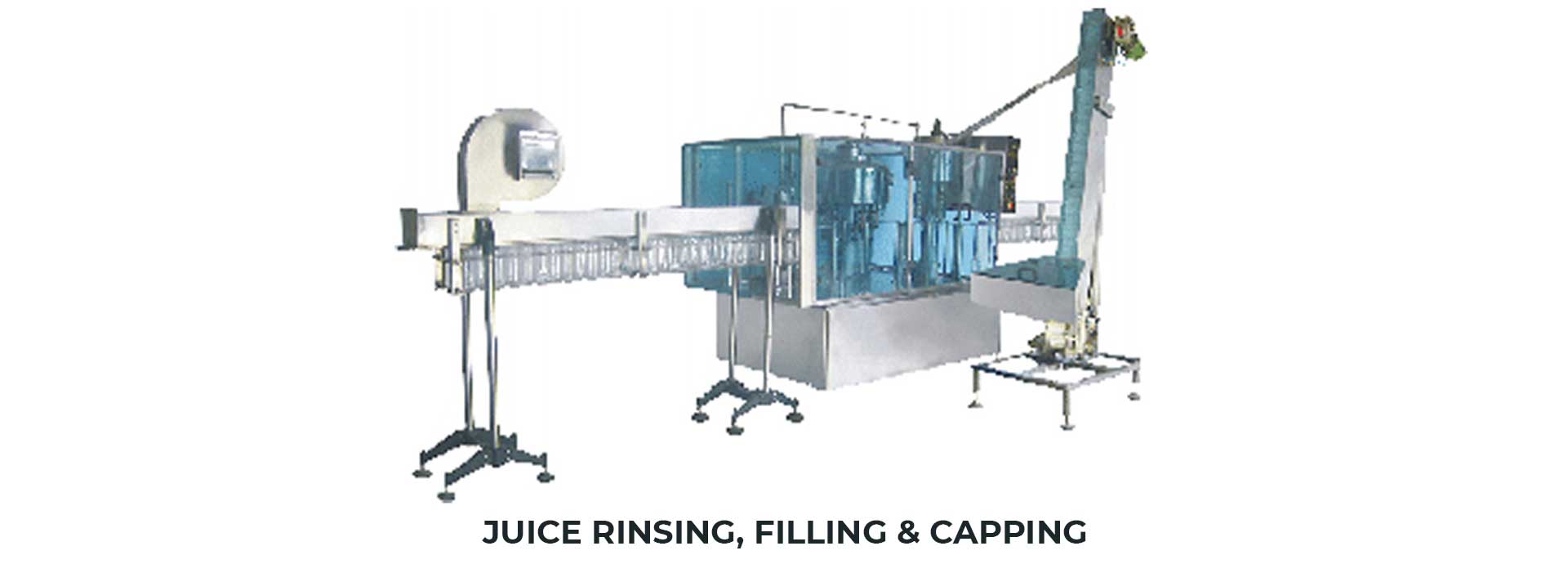
CARBONATED SODA SOFT DRINK PROJECT:
CSD RINSING, FILLING & CAPPING MACHINE:
Rinsing
Inside of bottles are rinsed by spraying water or air or both. Empty bottles are transferred into the rotary rinsing section by an inlet neck guide. The bottles are held from their neck and inverted by a guide rod along their axis. After being sprayed internally, the bottles continue to move inverted for a while to drain the rinse water, after which they are turned back to the upright position. The nozzles have “No Bottle – No Spray System” which is activated only by the presence of bottles, sensed at the in-feed spider. The option of attachment of a independent rinser machine is possible, to build a mono bloc machine of Rinser filler crowner / capper for bottles.
Filling
The filling operation is carried by CO pressure, by means of the latest state of the 2 art ULTRA VALVE (mechanical valve) which has a dual snift, one for pre-evacuation or flushing before filling the bottle, the other snift is for bottle head space snifting. This valve has complete CIP features. This valve fills at a very high speed due to the positive lift mechanism. An option of flow meter along with a pneumatic actuator valve (electronic filling valve) for extremely accurate fill can be the latest option.
Capping
Different capping heads can be installed on the mono-block machine to apply plastic screw caps, aluminium caps and metal crown corks. Two types of caps can be applied on the same machine in order to have capability to apply different closure.
WATER RINSING, FILLING & CAPPING MACHINE:
RFC series machinery a fully automatic multi-function combined machine integrating washing, filling & capping into single body. This machine is equipped with advance man machine inter-facial control technology with all necessary automation. It works hanging neck holding method hence very convenient bottle change over.
Sugar Syrup Preparation Tank For CSD, Sugar Filter Press For CSD, CIP System For CSD, PHE System For CSD, Carbonator For CSD, Carbonated Fruit Drink Pasteurizer, Warmer Tunnel For CSD.
1. SUGAR SYRUP PREPARATION TANK FOR CSD:
- Fro Storage / Blending / Dispensing / Standardization / Sugar Syrup Preparation.
- Suitable collect, store, dispense and blend liquids like pulp, juice, beverage, sugar syrup can be fitted with stirrer or blending device, temperature indicator, liquid level indicator and CIP spraying head.
- Tanks can be fabricated in SS 304 / 316 in single / double / triple layer with or without steam jacket insulation.
- The tanks are welded with smooth inner walls and are finished upto 150 grit finish and are hydraulic tested.
- Available in capacities from 100-L – 15-KL interconnected with centrifugal / screw pumps.
2. SUGAR FILTER PRESS FOR CSD:
The unfiltered liquid is fed into the filter under positive pressure, where liquid travels in downwards direction and finds its way through opening on sides of the filter plates. As the liquid pressure increases, the filter media holds the foreign particles and allows only clear filtrate to pass through the central channel formed by interlocking pressure cups to the outlet is reached or continued until the cake holding capacity of the unit is reached or until the filtrate rate becomes too slow owing to cake resistance.
- Horizontal plate filter press is enclose construction, preventing evaporation, oxidation, leakage and fumes escaping from product.
- Filter Plates are available in two sizes. Deep plate for large percentage of cake holding capacity and shallow plate for small percentage of cake holding capacity.
- The horizontal filter plate even thickness of cake prevents the cake dropping as well as cracking, thus assuring better filter quality.
- The Filtration area cake holding capacity can be increased or decreased according to requirement.
3. Herculean Packaging Solution
CIP system are supplied on frame mount with a wide range of capacities, CIP circuits, bespoke software and recipes, Herculean Packaging Solution CIP units are designed for 2, 3, or 4 tank systems and from 1 to 4 pressure lines depending on number of circuits and CIP requirements. Each pressure line include a CIP pump, circulation tank, heat exchanger, process valves, flow meter, conductivity meter, sensors and all necessary internal piping and wiring.
Herculean Packaging Solution
CIP unit automatically controls the cleaning time, detergent temperature, flow and concentration records these parameters continuously and for each cycle for tractability. Available semi & fully Automatic Models, Capacity as per Requirement.
4. PHE SYSTEM FOR CSD:
A plate heat exchanger is a type of heat exchanger that uses metal plates to transfer heat between two fluids. This has a major advantage over a conventional heat exchanger in that the fluids are exposed to a much larger surface area because the fluids spread out over the plates. This facilitates the transfer of heat, and greatly increases the speed of the temperature change. SS plate heat exchangers are made of 100% stainless steel and provide efficient heat transfer with a small footprint. They are maintenance free and provide a long service lifetime. They are suited in applications which put high demand on cleanliness, applications where aggressive Medias such as ammonia are used or where copper and nickel contamination is not accepted. Can handle very high temperatures or extremely high pressure.
5.CARBONATOR FOR CSD:
Advanced intermix carbonator ensures accurate proportional mixture of water, syrup and carbon dioxide duly controlled by screen. This ensures consistency in various batch mixes, taste & accurate mixture of Co2 gas. It can be interconnected within water / syrup chiller.
Available from 500 to 10,000 LPH Capacities
6. CARBONATED FRUIT DRINK PASTEURIZER:
A method for producing a carbonated juice beverage and carbonated fruit beverages produced according to the steps of providing a juice, typically a fruit juice, cooling and carbonating the juice, bottling the carbonated juice to from sealed bottles containing the carbonated juice and pasteurizing the carbonated juice in the sealed bottles.
7.WARMER TUNNEL FOR CSD:
It is used for the warming of PET bottle and glass bottle after the low temperature filling. The sectional design makes spray temperature zoning simple, through temperature control, it makes the product temperature rise section by section.
It aims to reduce the influence of the surface dew of low temperature filling bottle on labeling and packaging.
Process Flow: after low temperature filling, the bottle enters into the bottle warmer through multi-lane conveyor.
The warmer tunnel is used for getting cold bottles from 2 / 3 degrees to the room temperature of 30-35 degrees it is used for cold filled bottles like soft drink.
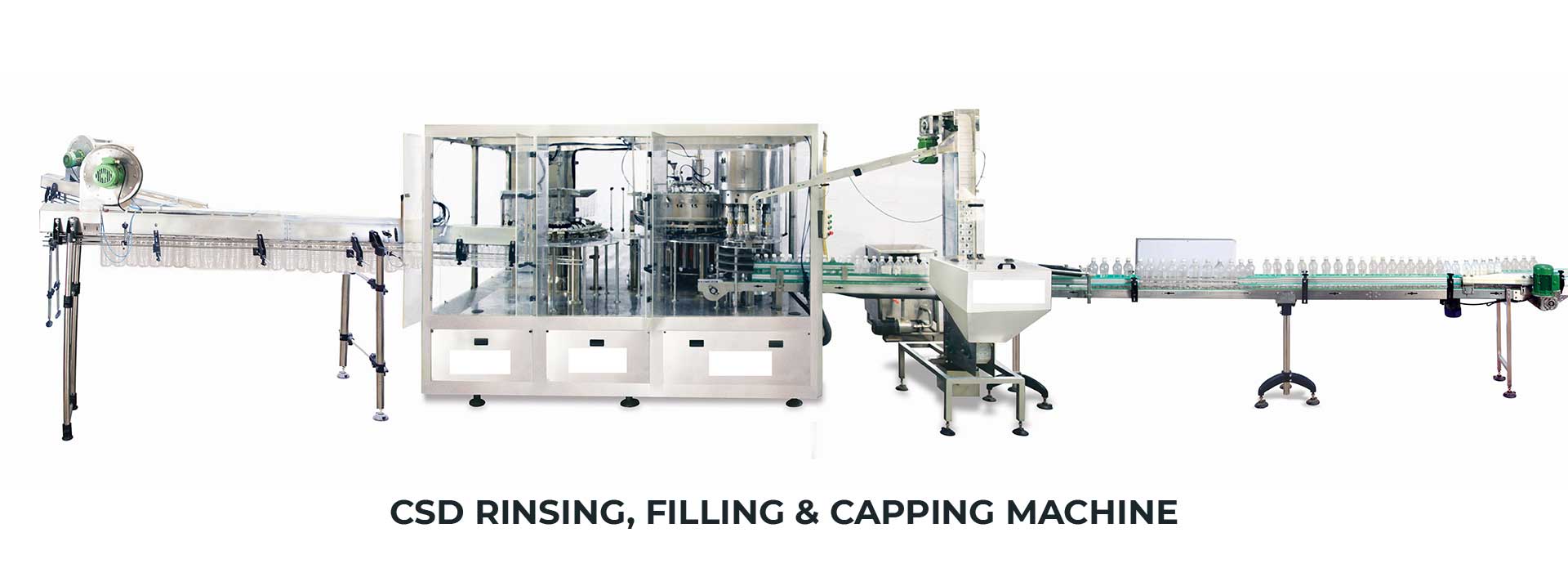
PACKAGING DRINKING WATER PROJECT
Flavour water plant, Mineral Water Project
1.MINERAL WATER PROJECT:
Assembled using quality raw material, the offered range is designed using modern technology and is capable of removing all the impurities from water. These are widely appreciated for their flawless filtration of contaminated water and make it entirely free from bacteria. The offered range finds their applications in various process industries. It kills the microorganisms and settles the impurities without disturbing the water balance. This system is acknowledged for features like easy usage, compact design and energy efficiency.
2.FLAVOUR WATER PLANT:
These Flavoured Waters Are Healthier than the Usual Sugary Sodas, Iced Teas and Lemonades — But They’re A Whole Lot More Exciting than Plain Old H20. Infused with Fresh Fruits, Vegetables and Herbs, They’re everything you Never Knew You Wanted in A Glass of Water.
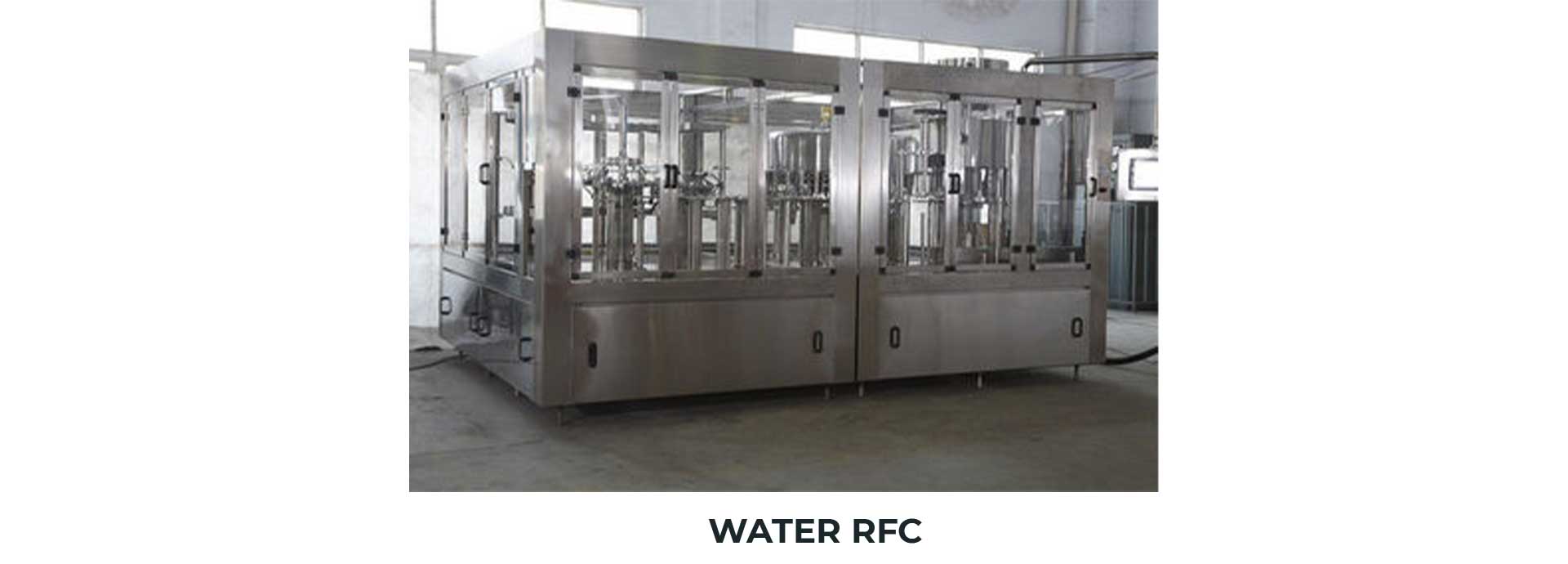
WATER TREATMENT PLANT
FRP Ro Plant: Agriculture Ro Plant, Iron & Hardness Removal System with Ro.
1.FRP RO PLANT:
- Self-encapsulated hollow fiber ultra-filtration membrane module (inside – out)
- Operating Mode: Dead-end or cross flow, Back washable.
- Module Mounting : Vertical.
- Nominal Membrane pore size : 0.02 Micron.
- Membrane Material: Hydrophilic PES.
- Housing Material: UPVC.
- End cap material: GRP.
- Nozzles Size: 2″ Victaulic.
2.AGRICULTURE RO PLANT:
- RO plant design based on Raw Water Quality.
- Treated Water Quality as per Requirement.
- Raw Water Feeding Pump.
- Pressure Sand Filter (FRP).
- Activated Carbon Filter (FRP).
- Micron Cartridge Filter Housing.
- Antiscalant Dosing Pump.
- Antiscaling Dosing Tank.
- High Pressure Pump.
- RO Membrane.
- Fiber – Reinforced Plastic Pressure Vessels.
- Pressure Gauges.
- Rota Meters.
- Control Panel – PLC Base.
- Pressure Switch.
- Stand For Unit.
- UPVC Interconnecting Pipe Lines.
IRON & HARDNESS REMOVAL SYSTEM WITH RO:
The presence of iron is probably the most common water problem faced by consumers and water treatment professional. The maximum contaminant levels for iron and manganese is potable water are 0.3 milligrams per lifter (mg / l) and 0.05 mg / l, respectively. Iron and manganese in excess of the suggested aximum contaminant levels usually result in discolored water and staining of fixtures and clothing.
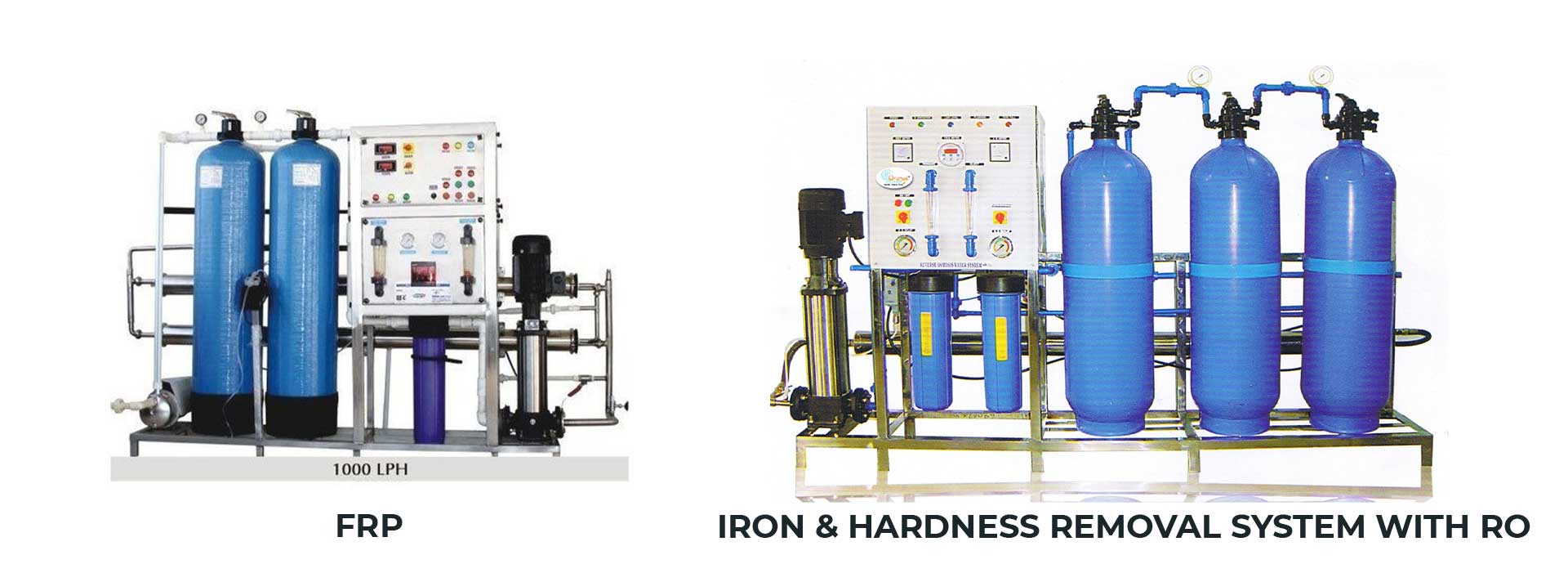
SHRINK-WRAPPING MACHINE
Fully Automatic Shrink-wrapping machine, Semi-Automatic Shrink-wrapping machine.
1. FULLY AUTOMATIC SHRINK-WRAPPING MACHINE:
- Power Supply: 440v, 3 phase with neutral.
- Max Film width: 550 mm.
- Max height of product: 375 mm.
- Film Type: LDPE.
- Air Consumption : As per Machine requirement.
- Power Consumption : As per Capacity.
- Programming PLC HMI.
- 4 Pneumatic cylinder.
2. SEMI-AUTOMATIC SHRINK WRAPPING MACHINE:
- Power Supply: 440v, 3 phase with neutral.
- Max film width: 550 mm.
- Max hight of product: 375 mm.
- Film Type: LDPE.
- Air Consumption: As per machine requirement.
- Power Consumption: As per Capacity.
- Dimensions: L-13.8 ft X W-3 ft X H-6 ft.
- 4 Pneumatic cylinder.
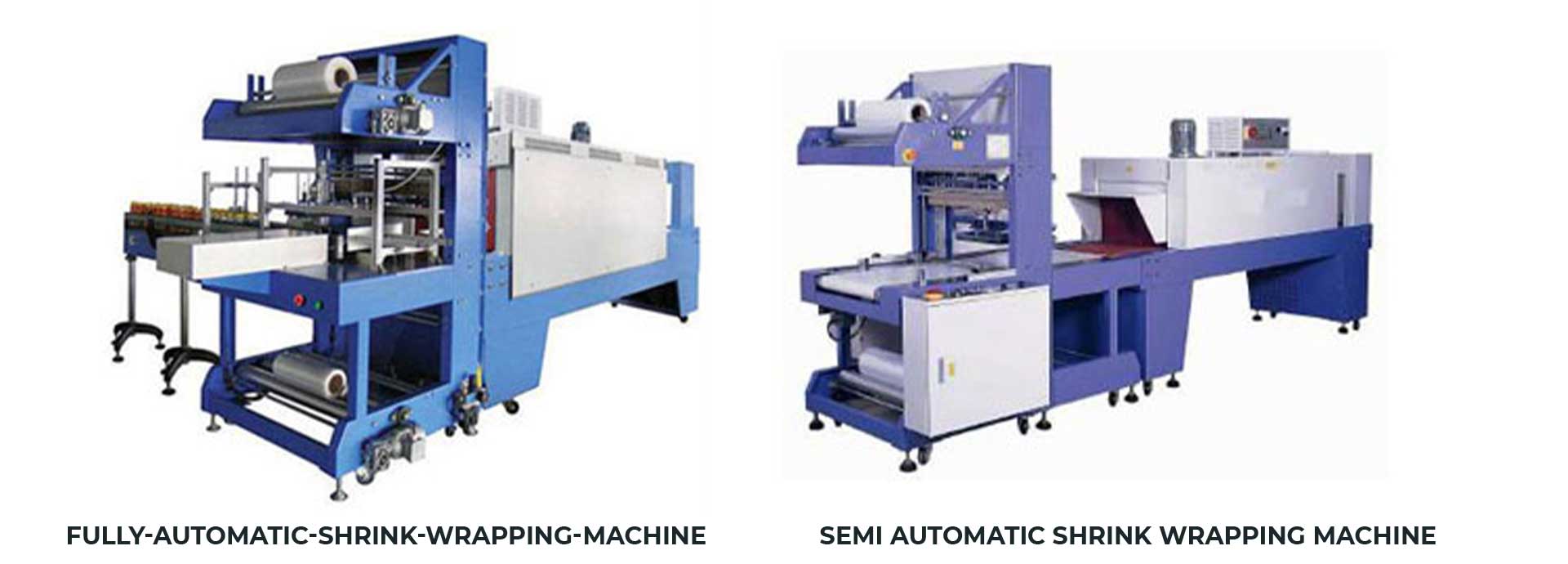
LABELING MACHINE
Bopp Labeling Machine, Sleeve Labeling Machine, Sticker Labeling Machine
1. BOPP LABELING MACHINE
- Output Speed : 60 / 90 / 120 / 150 / 200 / 250 / 300 & above BPM
- Bottle Diameter : As per Requirement
- Bottle Height : As per Requirement
- Size of Label: H 50 – 100 mm, L 160 – 295 mm.
- Diameter of label roll (mm) : As per label size.
- Power Supply: As per capacity.
- Machine Dimension (feet): As per Requirement.
2. SLEEVE LABELING MACHINE:
- Output: Up-to 60 / 90 / 120 BPM.
- Sleeve LFW : Min-75 mm, Max-165 mm.
- Sleeve cut Length : Not less than 40 mic.
- Inter lock : No Bottle – No Sleeve, Guard open – Machine off with respect to alignment / paneling.
- Contact Parts: SS-304 / Nylon / Aluminium.
- Drive : Stepper Motor Drive (For sleeve feeder & cutter)
- Controls: Programmable Logics Make: Delta.
- Power Consumption : As per capacity.
- Machine Dimension (Feet): As per Requirement.
3. STICKER LABELING MACHINE
- Label Height: 8 mm to 90 mm.
- Standard Label: 12 mm to Unlimited.
- Label Roll diameter: 300 / 400 mm.
- Core Diameter: 75 / 76 mm.
- Power Consumption: As per Capacity.
- Machine Dimension (Feet): As per Requirement.
- Speed: Up to 120 Labels per minute.
- Conveyor Height: 865 – 960 mm.
- Overall: 825 X 715 X 1550 mm.
